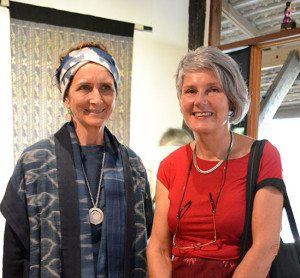
Just back from the most inspiring and wonderful Textile tour of Northern Thailand and Laos with Active Travel and Valerie Kirk. To see people weaving in almost every village is always inspiring and we visited many minority groups with their own specialty and styles of weaving, spinning, embroidery and dyeing.
Beginning in Thailand we visited Studio Naenna in Changmai where Patricia Cheesman presented an extensive talk on the range of textiles in her gallery. Patricia is author of Lao Tai Textiles – The Textiles of Xam Nuea and Muang Phuan and an authority on textiles from the region. What a difference it makes to have someone explain the story of a textile. They really are story books, not only in the symbolism of the design, but how the cloth was made and its social connections and reasons for existence. Patricia’s daughter Lamorna also presented on Indigo and other natural dyes, explaining about the ‘mother’ pot which was 25 years old and how the dye is used from it to continue dyeing.
My post here isn’t a lineal snapshot of my trip but rather a reflection of what stood out to me…but perhaps not others. This is the nice and sometimes disappointing thing about travel – I take myself and my own experiences to become submerged in something utterly new. Something that I can be unprepared for so I appreciate that other travellers on the trip helped me to see aspects of the experience which I may not have noticed except through their generous insights.
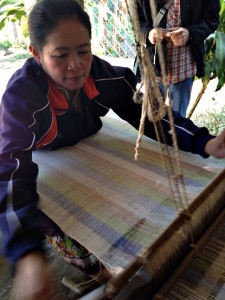
Spinning was what I was rather ‘hungry’ to see and here is a little video of Mrs Kong Seng at the TaiLue weaving centre in Oudomxai in Laos. The cotton is being spun with the long draw method and you may notice that the traditional wheel is built in such a way that its slant accommodates quite a comfy sitting position for the long periods of spinning which are necessary. We encountered much handspun fabric which entailed often growing the cotton then ginning, prep for spinning, then dyeing before weaving. The TaiLue weaving centre was producing small production runs of fabric with colours and the aesthetic for the Japanese market. The handspun cotton in plain weave was particularly lovely and has left me with a renewed respect for the handspun singles cotton in weave. I really like seeing small production enterprises of this type because in some form it’s closer to how I work without the social dimension of village weaving.
In the village of Ban Nam Dee in Luang Namtha we heard the overpowering noise of an automated cotton ginning machine. I would think this was a substantial investment for the weavers to process the cotton more efficiently although the noise was certainly the occupational hazard. Other spinning of interest was of the Kheuapiad, jungle vine. Traditionally the Khmu, indigenous people of Northern Laos, have created string bags from this processed and spun vine. Although these types of bags (Billum from PNG) are often thigh spun with a continuous supply of fibre to create the bag, this vine is knotted with a splice/overlap to make the lengths. The many ‘bumps’ are almost imperceptible in the fine work and I find out that this type of knotting isn’t unknown (also used in Japan). See how the bag is created here. See below how the twine is create via PMC of Oudomxai – a co-operative supporting local traditional creators and crafts.
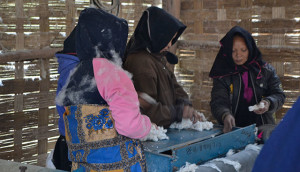
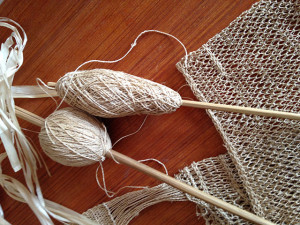
Leave a Reply