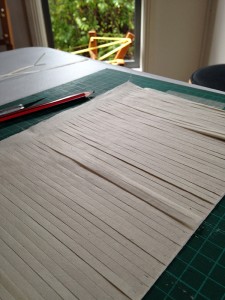
There is a magnetism in paper yarns for weaving and I have had many goes at it. I am probably more interested in actual spun paper yarn than the rolled or folded paper approach but they all have their particular benefits in creating a woven structure.
When I was in Kyoto last year I bought a few sheets of Kozo paper for creating spun thread (kami-ito) for weaving (Shifu). In Japan this is considered the very best handmade paper for this purpose and the traditions and skills attached to the whole papermaking and yarnmaking process are formidable and quite different to the traditions of paper twine from Europe. For more info on the tenacity and dedication to creating Kami-ito (paper threads for weaving Shifu) see “A Song of Praise for Shifu“ by Susan J. Byrd. Another good recent publication is “Kigami and Kami-ito“ in English and Japanese. Also a great book for a broader overview of European paper yarn history and the comparison to Japanese thread making with ideas for creating paper thread textiles in Paper Textiles.
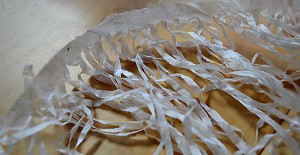
Sometimes reading too much can make me thoroughly daunted and ‘scared’ of attempting such a feat on the most perfect paper you’ve ever seen and unlikely to ever see again. But then it’s a step closer to understanding the process than having exquisite paper sitting in my studio cupboard.
I was pretty happy with the resulting yarn considering my fears, and I must say that working with paper of this standard was amazing. As any spinning is – it gets you closer to that real source of the natural.
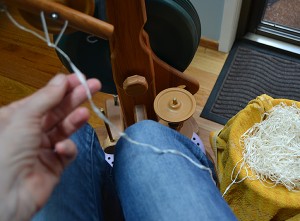
Here are the basic steps in the process. Firstly, preparing the paper by folding it in a simple three fold concertina fashion then marking off 5mm strips. Threads in Japan are cut much thinner but 5mm was a good starting point for me. Next cutting the paper through all of the layers with a blade leaving a uncut edge which forms the paper turn and the continuous thread.
I then left the cut paper overnight in a dampish cloth. This is where the human intuition comes into play. From this point the paper needs to be treated as a new baby when you first hold them in your arms. Intensely aware of their needs and comfort at every turn. At least that’s what it seemed to me. And I overdid it with too much dampness at one point! So, lucky it wasn’t a baby.
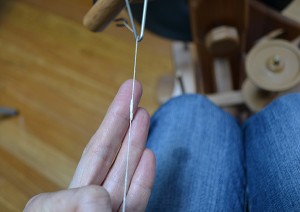
Then I rolled the yarn. This requires far more skill than I have at this point but I managed a light rolling. This rolling process should just about create yarn of the strips but I did a crumpling that still allowed me to spin it into yarn. The next step is the tearing of the entire cut sheet into one continuous strip ready for spinning.
The final spinning process on the wheel was an absolute delight and the joins spun a lovely bump throughout.
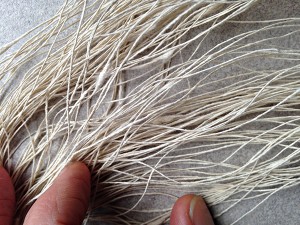
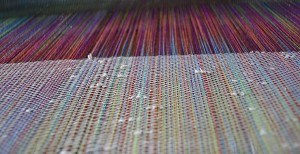
Leave a Reply